Cost-efficient and defect-free forming of aerospace composite components
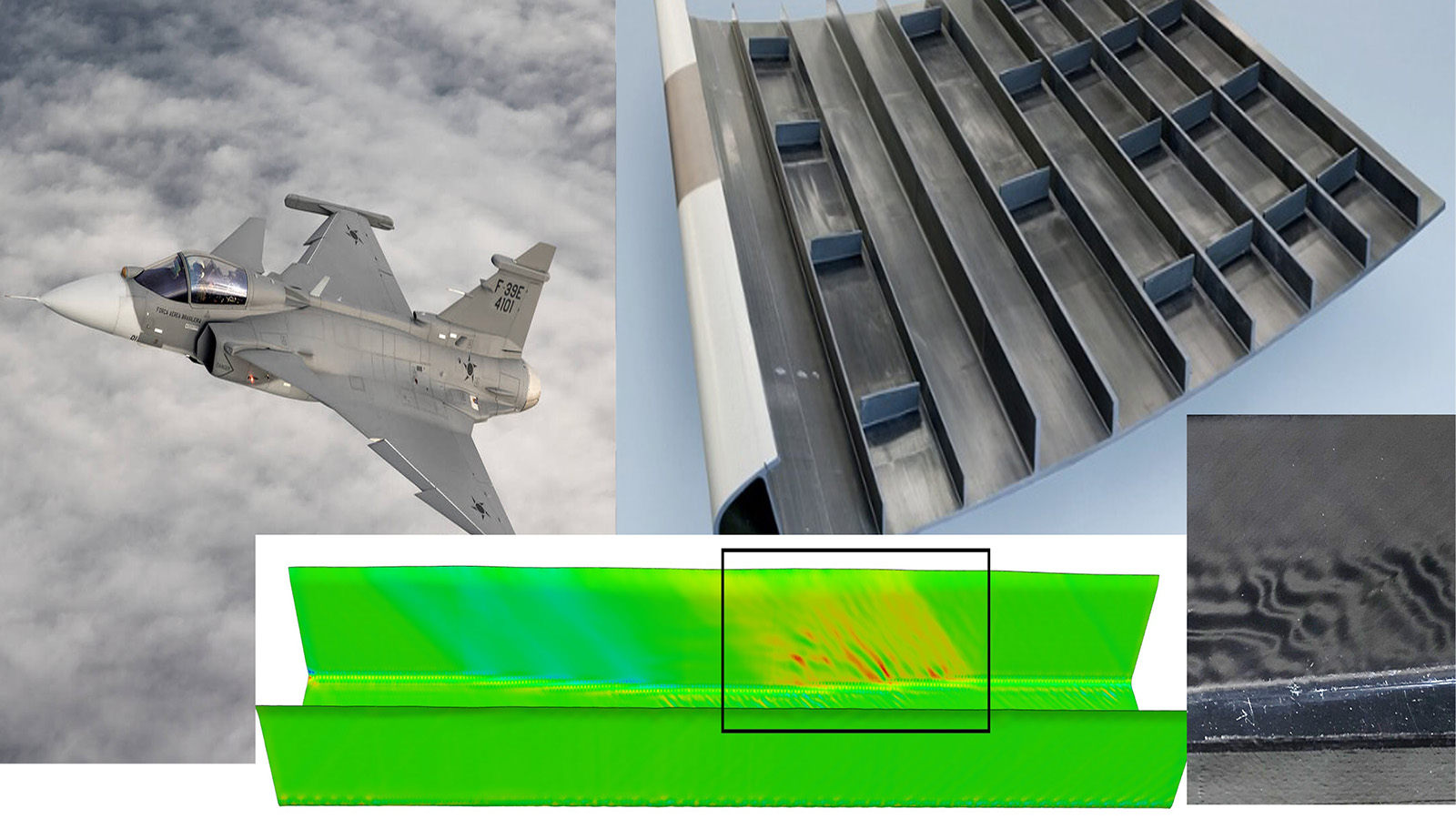
Based on numerical simulations and targeted experimental studies, KTH and Saab have identified the underlying causes of critical material discrepancies that arise during the multi-layer forming of advanced composite materials for aircraft components. The findings highlight that a methodology for fault-free forming must be integrated already at the material design stage.Today, the wing spars produced for the Saab Gripen E fighter successfully incorporate the results of this research. The methodology also serves as a foundation for manufacturing high-quality composite parts for civil aircraft.
Background
The use of lightweight materials is essential in modern aircraft design. Over 50% of the structural weight of modern civil aircraft, and many critical structural components of fighter jets, is made up of thin layers (0.1–0.3 mm) of pre-impregnated (prepreg) carbon fibres, which are stacked to form composite laminates. To meet the varying load requirements throughout the aircraft, these fibres are oriented in specific directions, allowing for tailored mechanical properties.
However, producing an optimally designed composite structure is often challenging. Draping stacks of thin laminates into complex 3D geometries without introducing wrinkles or undesirable resin flow phenomena is non-intuitive.
The Hot Drape Forming (HDF) method offers a cost-efficient solution by enabling the forming of stacked prepreg layers with more than two fibre orientations, into complex shapes in a single operation. This technique takes advantage of the interactions between individual layers during the forming process. By tailoring these interactions, the processing window of the method can be significantly expanded.
Project Aim
The aim of the project was to develop the HDF method to reduce forming faults, expand its processing window, and simplify the implementation of novel material systems. This was pursued through the following objectives:
- Experimental characterisation of the forming behaviour of single prepreg layers
- Development of a forming simulation tool to describe the deformation of individual layers and the interactions between them
- Experimental verification at the micro-, meso-, and macro-scale levels